Cutting Machines: Types, Applications, Usage, and Precautions
Introduction
Pipe cutting machines, often referred to as tube cutting machines, play a crucial role in various industries where precision cutting of pipes, tubes, and other cylindrical materials is required. Whether in the construction of buildings, the manufacturing of automobiles, or the production of pipelines for oil and gas, the accuracy, speed, and efficiency provided by modern pipe cutting machines are indispensable. This article explores the different types of pipe cutting machines, their applications, usage methods, and precautions.
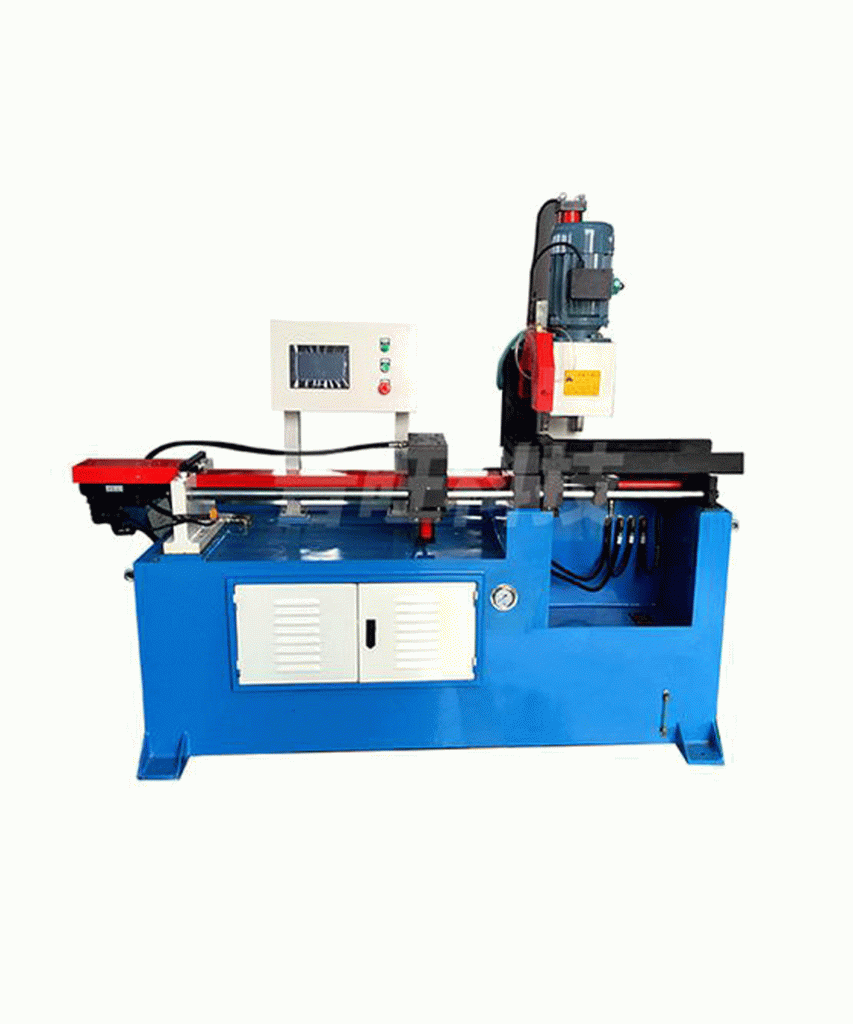
Types of Pipe Cutting Machines
Pipe cutting machines come in various types, each designed for specific materials, cutting methods, and levels of precision. The most common types include:
- Rotary Pipe Cutting Machines
Rotary pipe cutting machines use a rotating cutting tool (often a blade or abrasive disc) to slice through pipes. These machines are typically designed for cutting metal, plastic, and composite pipes. The cutting tool moves around the circumference of the pipe, ensuring a smooth, accurate cut. Rotary cutting machines are ideal for high-volume production and are commonly used in the automotive and plumbing industries.
- Advantages: High cutting speed, precision, and minimal burr formation.
- Applications: Automotive manufacturing, plumbing, HVAC systems, and pipeline construction.
- Band Saw Pipe Cutters
Band saw pipe cutters utilize a continuous loop of band saw blades to cut pipes. These machines are known for their ability to handle a wide range of materials, from soft metals like aluminum to harder metals like stainless steel. The band saw’s continuous motion allows for efficient, straight, or angled cuts.
- Advantages: Versatile cutting capabilities, suitable for a variety of materials and pipe sizes.
- Applications: Manufacturing, heavy industry, and fabrication shops.
- Cold Saw Pipe Cutting Machines
Cold saw pipe cutting machines use circular blades made of high-speed steel (HSS) or carbide to cut through pipes without generating excessive heat. The cutting process is slower than other types of saws, but it provides high-precision cuts with minimal heat-affected zones, which is essential for certain materials that can deform due to heat.
- Advantages: Clean, precise cuts with minimal burrs and heat distortion.
- Applications: Precision engineering, aerospace, and metalworking industries.
- Laser Pipe Cutting Machines
Laser cutting machines utilize high-powered lasers to cut through pipes with extreme precision. The laser beam melts the material along the cutting path, and the molten material is blown away by a gas jet. Laser cutting machines can handle complex geometries, including intricate holes and curves, which makes them ideal for specialized applications.
- Advantages: Extremely precise, capable of cutting complex shapes and intricate patterns.
- Applications: Aerospace, medical equipment manufacturing, and automotive industries.
- Plasma Pipe Cutting Machines
Plasma cutting machines use a plasma torch to cut through conductive materials, such as metals. The high-temperature plasma stream melts the metal, and the force of the plasma removes the molten material, creating a cut. Plasma cutting is fast and efficient, especially for thicker materials.
- Advantages: Speed, versatility, and ability to cut thick materials.
- Applications: Metal fabrication, construction, shipbuilding, and pipeline construction.
- Shear Cutting Machines
Shear cutting machines operate by using a scissor-like action to slice through pipes. The machine employs a pair of blades that move in opposite directions to create a clean cut. Shearing machines are typically used for cutting thin-walled pipes or tubes.
- Advantages: Fast cutting, clean edges, and minimal waste.
- Applications: Manufacturing of thin-walled pipes, sheet metal fabrication.
- Water Jet Pipe Cutting Machines
Water jet cutting uses a high-pressure stream of water mixed with abrasive materials to cut through pipes. This type of cutting method does not generate heat, making it ideal for materials that are sensitive to thermal damage. Water jet machines are also highly accurate, with fine tolerances.
- Advantages: No heat distortion, extremely precise, and can cut a variety of materials.
- Applications: Aerospace, automotive, electronics, and food industries.
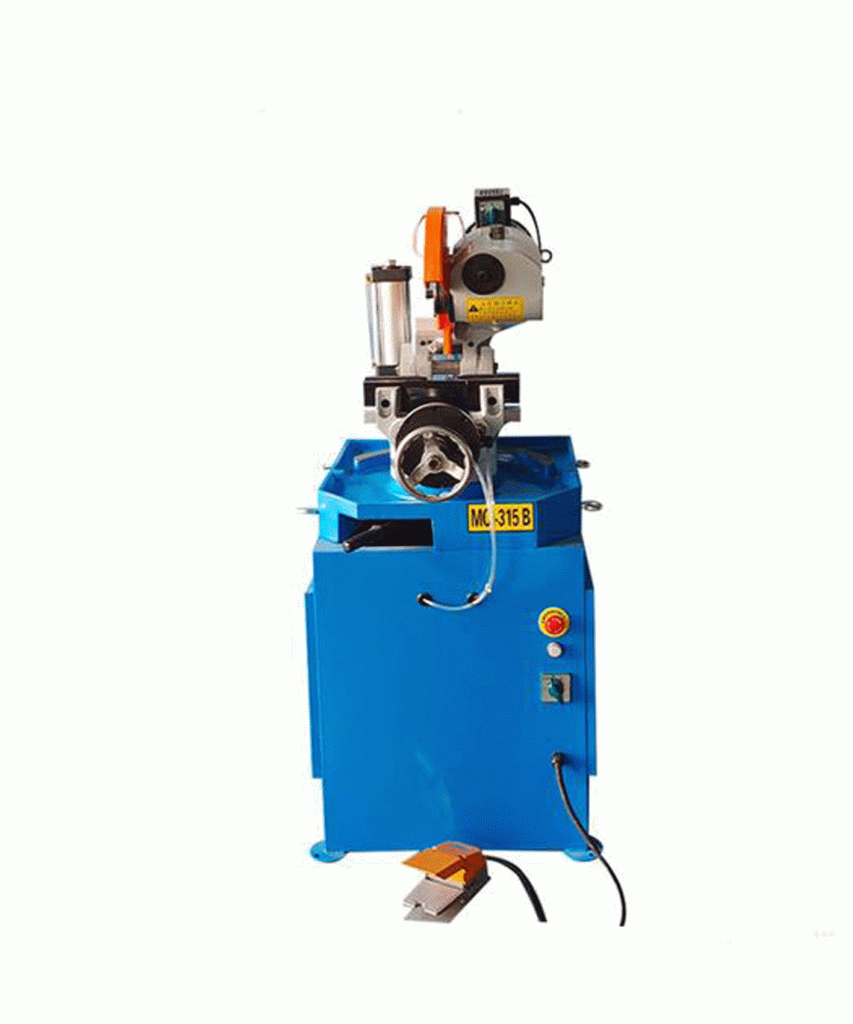
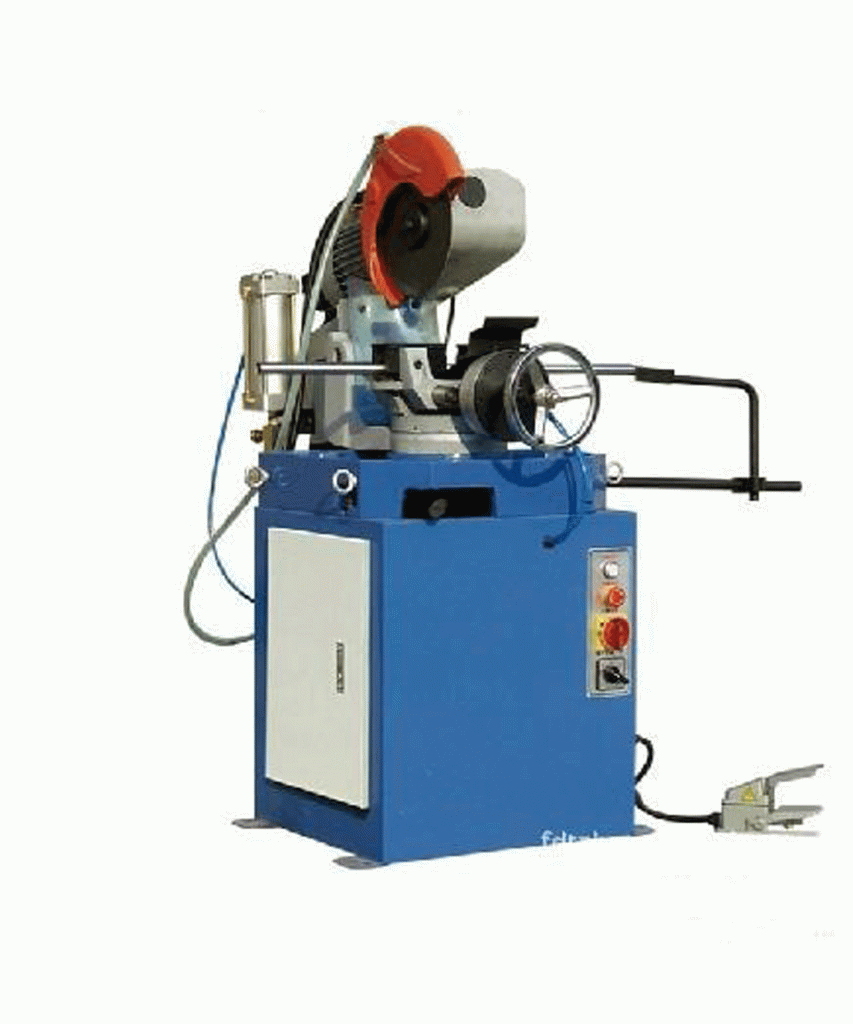
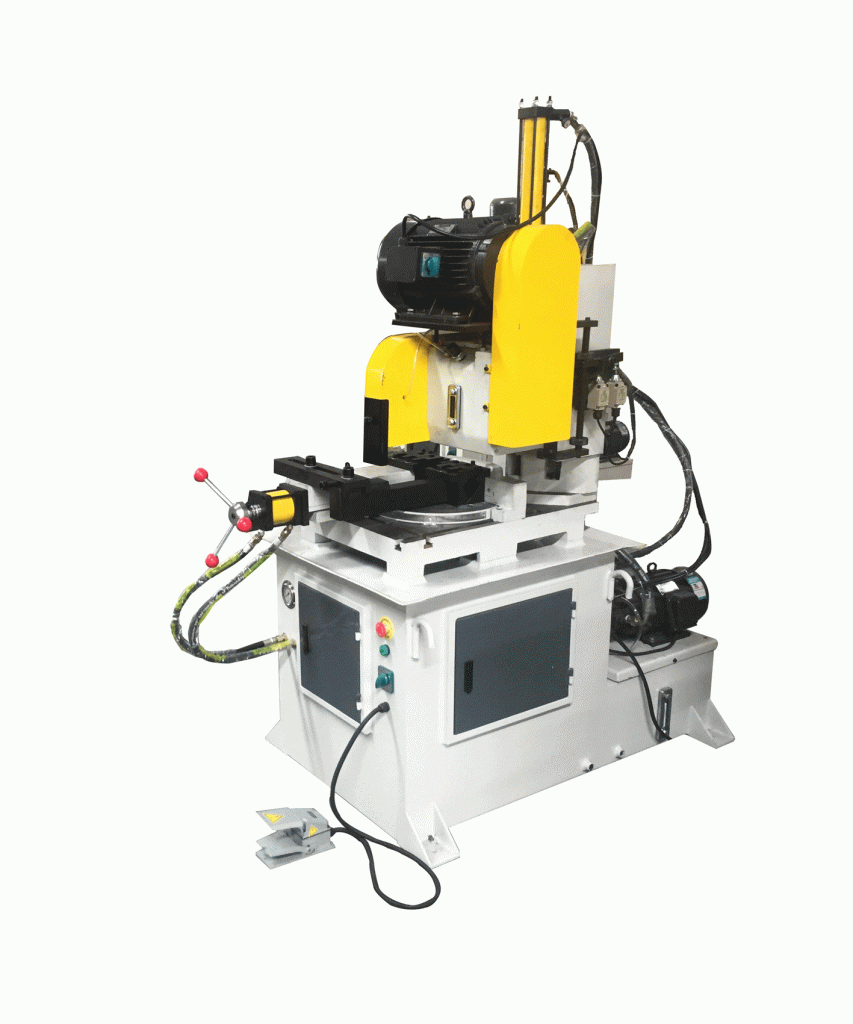
Applications of Pipe Cutting Machines
Pipe cutting machines are utilized across a wide range of industries due to their ability to cut pipes and tubes precisely and efficiently. Here are some common applications:
- Construction and Plumbing: In construction and plumbing, pipes need to be cut to specific lengths and angles for installation in buildings, homes, and infrastructure. Pipe cutting machines make the task faster and more accurate than manual methods.
- Automotive Industry: In automotive manufacturing, pipes are often used in the creation of exhaust systems, fuel systems, and HVAC systems. Cutting machines ensure these pipes are precisely cut to fit into complex automotive designs.
- Oil and Gas: In the oil and gas industry, pipes are used for transporting fluids over long distances. Pipe cutting machines are used to cut pipes to the desired lengths during installation or maintenance, ensuring they fit perfectly in pipeline systems.
- Aerospace: Aerospace applications require high-precision pipe cutting for various systems, including fuel lines, hydraulic lines, and air conditioning systems in aircraft. The accuracy and cleanliness of cuts made by laser or cold saw pipe cutting machines are essential in these industries.
- Medical Equipment: In the medical equipment industry, precision cutting of tubes and pipes is crucial for creating components such as breathing tubes, catheters, and surgical instruments. The high precision of laser or water jet cutting machines is preferred in these scenarios.
- Shipbuilding: In the shipbuilding industry, pipes are often used in the construction of ships for water and fuel systems. Plasma cutting and band saw machines are commonly employed to cut these materials efficiently.
How to Use Pipe Cutting Machines
Using pipe cutting machines involves several steps, regardless of the machine type. Here’s an overview of the general procedure:
- Preparation and Setup:
- Before starting, ensure that the pipe cutting machine is properly set up for the specific task. This involves selecting the correct cutting tool or blade for the material and ensuring that the machine is calibrated for the desired cutting speed, pressure, and angles.
- Secure the pipe firmly in place using clamping or feeding mechanisms to prevent it from moving during the cutting process.
- Operation:
- Activate the machine, ensuring all safety precautions are in place. Feed the pipe into the cutting area, where it will be cut according to the settings. Many machines, especially CNC-controlled ones, require minimal manual intervention during the cutting process.
- In automated machines, the pipe cutting process is controlled via a program that adjusts the speed, pressure, and angle for different tasks.
- Post-Cutting Inspection:
- After the cutting process, inspect the pipe for accuracy and quality. Depending on the material, some finishing work may be required to smooth the edges or remove burrs.
- Maintenance:
- Regular maintenance of the cutting machine is crucial for maintaining precision. This includes cleaning, checking for wear and tear, and replacing parts like blades, nozzles, and filters as needed.
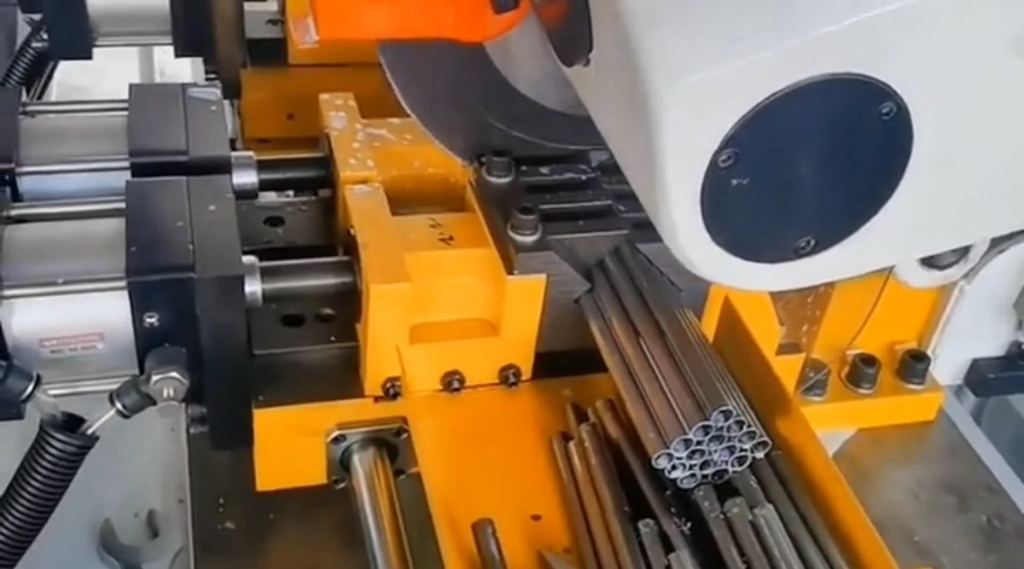
Precautions When Using Pipe Cutting Machines
While pipe cutting machines are highly effective, operators must follow several precautions to ensure safety and optimal performance:
- Safety Gear: Always wear appropriate personal protective equipment (PPE), including safety goggles, gloves, ear protection, and protective clothing, to safeguard against debris, high temperatures, and noise.
- Proper Setup: Ensure the machine is properly calibrated and that the pipe is securely clamped to avoid movement during cutting, which could lead to inaccurate cuts or accidents.
- Regular Maintenance: Perform routine maintenance on the cutting machine to ensure consistent performance. This includes checking for worn-out parts, ensuring that blades or tools are sharp, and lubricating moving parts to prevent overheating or mechanical failure.
- Material Compatibility: Use the correct cutting tools and settings for the material being cut. For example, different materials like metal, plastic, or composite pipes require different cutting methods and tools.
- Avoid Overloading: Do not overload the machine or attempt to cut pipes that exceed the recommended size or thickness. Overloading can lead to equipment damage, poor-quality cuts, and even safety hazards.
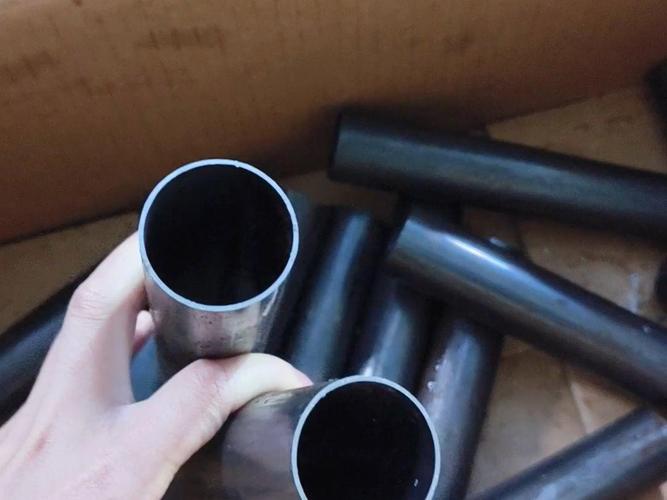
Conclusion
Pipe cutting machines are essential tools in industries where precision and efficiency are paramount. With various types available, from rotary and band saw cutters to laser and plasma cutters, these machines offer solutions for a wide range of applications. By understanding the different types of pipe cutting machines, their applications, usage methods, and precautions, manufacturers can enhance productivity, ensure high-quality results, and maintain safe working conditions in their operations.